Case Study Review: Drilling Mud Additives
- B0
- Oct 20, 2018
- 2 min read
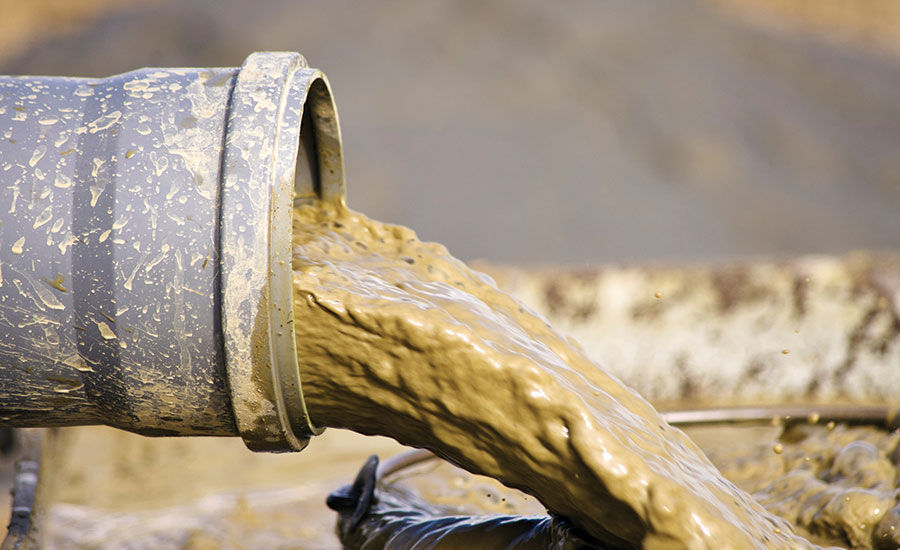
Drilling mud is an imperative component of drilling and maintaining a robust reservoir. It can serve multiple purposes simultaneously: from balancing formation pressures, to keeping the drill bit from torquing and/or damaging.
A challenge for drilling engineers is the accurate and pertinent choice for the properties of the drilling mud or the additives being used. Every unique well requires a unique blend of drilling mud to meet all the challenges faced in the subsurface environment. This blend is dynamically affected as the well depth increases. Different formations, temperatures, pressures, all demand suitable drilling fluids.
Saline, clay, limestone, and dolomite formations, which are very common to encounter in a well, all require vastly different properties of drilling mud. To use appropriate blends of drilling muds which suit the formations and the reservoir properties is a very crucial job for the engineer.
One such unique formation in the Gulf of Thailand presented A HPHT (High Pressure High Temprature) well which required a unique drilling fluid at depths of over 10,000 ft. At high temperatures, rheology of fluids dictates that the fluids decrease in viscosity and density. This decrease can cause a loss in hydrostatic pressure and subsequently cause infiltrations from the formations to the well. Conversely, trying to compensate for the reduction in hydro static pressure can cause possible fluid loss in upper formations with a lower structural pressure.
The multitudes of conditions in this deep well required technical expertise to concoct the right balance in additives to gain suitable gel strength as well as stable emulsions. Apart from fluid loss, another hinderance the HPTT well posed was the reduction in mud viscosity. Reduction in mud viscosity could cause failure of drilling cutting transportation, and possible bottom-hole blockage, which could cause the drill bit to torque and could also damage the bottom hole equipment.
The engineers at Schlumberger used MUL XT* high temperature emulsifier, along with VERSAGE HT* high-temperature viscosifier to mitigate the rheological changes. To counter the mud loss, ONE-TROL additive was used. ONE-TROL is a slightly acidic amine-treated tannin, which has been used for many HPHT wells to reduce fluid loss[2]. This specific additive is also being used by Schlumberger in the North Field to assist Norwegian drilling companies.[4]
The final results after the treatment were very favourable. Recondition the mud was not found to be necessary which also saved 17.5 hours of tripping time[1]. The overall stability of the drilling mud before and after logging was positive as expected.

Source:
Schlumberger ltd.,"ONE-TROL Additive Saves 17.5 Hours of Rig Time in
HPHT Logging Operation, Gulf of Thailand",
[2]https://www.slb.com/-/media/Files/miswaco/ps-drilling-fluids/one_trol_ht.pdf?la=en&hash=3DE79C030034B5F7527572EBA13A0645CB2F4033
[3]https://www.slb.com/services/drilling/drilling_fluid/df_systems/nonaqueous_drilling_fluid_systems/versaclean.aspx
[4]https://www.slb.com/resources/case_studies/miswaco/one_trol_norway.aspx
October 2018, Web. Accessed 20 October 2018
Comments